What Factors Cause Pressure Sensor Malfunction and Failing
In the use of the pressure sensor, some factors will easily cause malfunction or failing to the sensor if these factors are not be avoided. This article summarizes six factors that are prone to pressure sensor failures, helping users solve malfunction and avoid malfunction in a timely manner.
For example, if the pressure sensor is installed close to the steam line that produces steam, its dynamic performance will be affected. A correct and simple solution is to transfer the pressure sensor to a location far from the steam line.
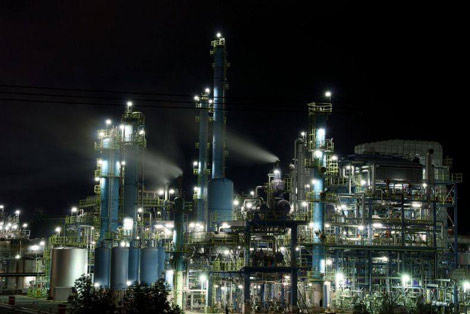
Other sources of EMI/RFI that need to be avoided include contactors, power cords, computers, walkie-talkies, cell phones, and large machines that produce varying magnetic fields. The most common methods for reducing EMI/RFI interference are shielding, filtering, and suppression.
The easiest way is to install the pressure sensor as far as possible from the obvious shock and vibration sources. Another possible solution is to use a vibrating isolator, which is depends on its installation.
If the pressure value occasionally reaches the upper pressure limit, the pressure sensor can withstand and return to its original state. However, when the pressure value reaches the rupture pressure, which will cause the diaphragm or casing of the pressure sensor to rupture, causing leakage. The pressure value between the upper pressure limit and the burst pressure will cause permanent deformation to the diaphragm, then causing output drift.
In order to avoid pressure overload, the user must understand the dynamic performance of the system and the limits of the pressure sensor in the use. In addition, the relationship between the components of the pump, control valve, balancing valve, check valve, pressure switch, motor, compressor and storage tank must be mastered.
-
Temperature cause malfunction to pressure sensor
For example, if the pressure sensor is installed close to the steam line that produces steam, its dynamic performance will be affected. A correct and simple solution is to transfer the pressure sensor to a location far from the steam line.
-
Voltage spike cause malfunction to pressure sensor
-
Fluorescent lighting cause malfunction to pressure sensor
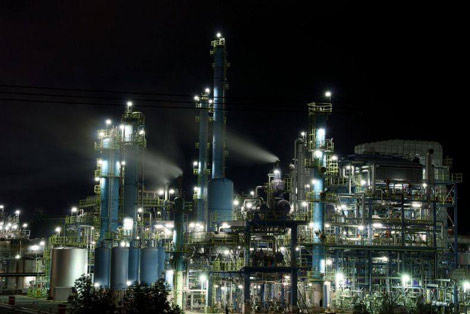
-
EMI/RFI cause malfunction to pressure sensor
Other sources of EMI/RFI that need to be avoided include contactors, power cords, computers, walkie-talkies, cell phones, and large machines that produce varying magnetic fields. The most common methods for reducing EMI/RFI interference are shielding, filtering, and suppression.
-
Shock and vibration cause malfunction to pressure sensor
The easiest way is to install the pressure sensor as far as possible from the obvious shock and vibration sources. Another possible solution is to use a vibrating isolator, which is depends on its installation.
-
Pressure overload cause malfunction to pressure sensor
If the pressure value occasionally reaches the upper pressure limit, the pressure sensor can withstand and return to its original state. However, when the pressure value reaches the rupture pressure, which will cause the diaphragm or casing of the pressure sensor to rupture, causing leakage. The pressure value between the upper pressure limit and the burst pressure will cause permanent deformation to the diaphragm, then causing output drift.
In order to avoid pressure overload, the user must understand the dynamic performance of the system and the limits of the pressure sensor in the use. In addition, the relationship between the components of the pump, control valve, balancing valve, check valve, pressure switch, motor, compressor and storage tank must be mastered.