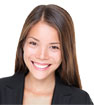
Pressure Sensor
Home » FAQ
It is well known that pressure transducers can be classified into absolute pressure transducers, gauge pressure transducers and differential pressure transducers depending on the type of measured pressure. In this paper, the absolute pressure transducer is compared with the gauge pressure and differential pressure transducer. The reasons for the zero drift of the absolute pressure transducer are analyzed from the aspects of principle, practical application and operation.
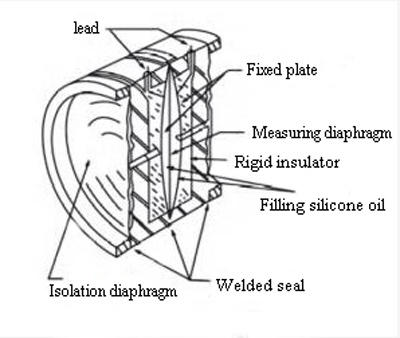
The application environment of the pressure transducer is very complicated. Therefore, both the pressure transducer and the measured object are in a disturbed environment at the same time, and inevitably suffer from external interference. Electromagnetic interference will cause hazards such as misuse, loss of information, leakage, equipment failure, and damage, etc. So, what should we do in the face of this situation? It requires consideration of the electromagnetic compatibility of the pressure transducer. Electromagnetic compatibility refers to the ability of equipment and systems to function properly in an electromagnetic environment and does not constitute unacceptable electromagnetic interference to other equipment in the environment.
There are many kinds of threads for pressure sensors. NPT, PT, G, and M are common in use and they are all pipe threads.
Metric threads are expressed as pitch. American threads and inch threads are expressed as the number of threads per inch. This is the biggest difference between the two. The metric thread is a 60-degree equilateral tooth, the inch thread is an isosceles 55-degree tooth, and the American thread is 60 degrees. Metric threads are used in metric units. American threads and inch threads are used in imperial units.
The pipe thread is mainly used for the pipe connection, and the inner and outer threads are closely matched. There are two kinds of straight pipe and tapered pipe. The nominal diameter refers to the diameter of the pipe to which the thread is connected. It is obvious that the diameter of the thread is larger than the nominal diameter.
Metric threads are expressed as pitch. American threads and inch threads are expressed as the number of threads per inch. This is the biggest difference between the two. The metric thread is a 60-degree equilateral tooth, the inch thread is an isosceles 55-degree tooth, and the American thread is 60 degrees. Metric threads are used in metric units. American threads and inch threads are used in imperial units.
The pipe thread is mainly used for the pipe connection, and the inner and outer threads are closely matched. There are two kinds of straight pipe and tapered pipe. The nominal diameter refers to the diameter of the pipe to which the thread is connected. It is obvious that the diameter of the thread is larger than the nominal diameter.
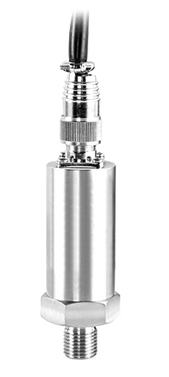
Factors such as temperature and mechanical stress will have negative impact on the long-term stability of the pressure sensor. However, in the production process, users can minimize the impact by regular testing. Manufacturers usually specify the long-term stability of the pressure sensor in a data sheet. The values given in these data sheets are determined under laboratory conditions, which refer to the expected maximum change in the zero point and output range throughout the year. For example, a long-term stability of ≤0.2% FS/year means that the total error of the pressure sensor will decrease by 0.2% of the total scale within one year. Pressure sensors usually take some time to "stabilize". As mentioned earlier, the zero point and sensitivity (output signal) are the main factors mentioned here. Users often notice the zero drift of the pressure sensor as they are easy to identify and adjust.
Differential pressure sensor is a kind of instrument widely used in industrial production. It can measure many physical parameters. The pressure of gas and liquid can obtained by differential pressure sensor, which is of great significance for industrial production.
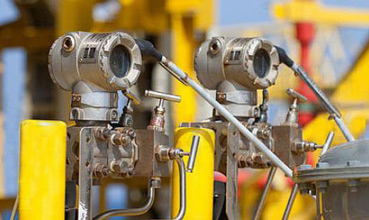
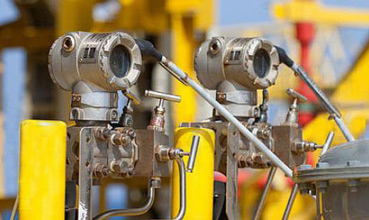
The pressure transducer select 4-20mA as the output signal mainly considering the comprehensive reasons of the three aspects. The first one is safety, the second is using a current source to transmit signals better than the voltage source; the third is the choice of current starting and ending point. The 4-20 mA signal system is an analog signal standard developed by the International Electrotechnical Commission (IEC) for process control systems. As product technology is increasingly innovated, the output signals of pressure transducers are increasingly diversified to suit different production needs. Despite it, most pressure transducers have 4-20mA output signals and other types of signals for users to choose.
The zero drift of the pressure sensor refers to the phenomenon that when the amplifier input is short-circuited, an irregular, slowly changing voltage is generated at the output. The main cause of zero drift is the effect of temperature changes on transistor parameters and fluctuations in supply voltage. In most amplifiers, the zero drift in the front stage has the greatest influence. The more the stages number and the larger the magnification, the more serious the zero drift.
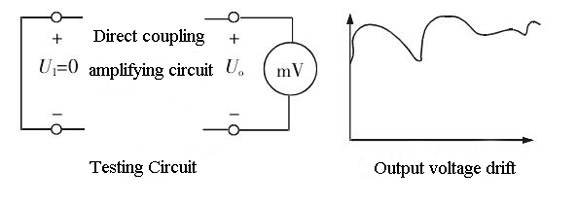
Pressure sensors using RS485 output signal are getting more and more applications in practical work, which is due to the development of pressure sensors in the direction of intelligence and digitization. At the same time, due to the simple design, convenient implementation and low price of the RS485 bus output circuit, it has a wide range of applications in pressure sensors and differential pressure sensors. However, due to various interferences at the engineering site and failures of communication nodes, stability problems in data transmission and reception will occur. At the same time, in the case of multi-machine communication, the failure of one node will cause the entire bus communication to collapse. Therefore, how to ensure the stability in the communication of the RS-485 bus output becomes a problem that needs to be focused on.
When selecting a right pressure sensor, it is important to understand the high temperature that will occur during actual use. If the measurement technique in use have no sufficient temperature compensation, it is most likely to cause serious errors and other risks. That is why the end users of pressure sensors need to know in advance the temperatures expected in their own specific application. There are two values need to be considered, that is medium temperature and ambient temperature. Both of these values are important. The medium temperature is the temperature at which the pressure port of the pressure sensor is exposed. The ambient temperature is the value produced in the environment surrounding the application and ultimately affects the electrical connection. The definition of the two values are different and their effects on pressure sensors are different.
In the pressure sensor application, there are many factors that affecting the measurement accuracy. Due to the overall design of the industrial site, the pressure sensor can not be installed near the measuring point in the use site, but is pressed to a more concentrated place through the pressure pipe to facilitate maintenance and management. This will result in a height difference between the measuring point and the mounting point. The pressure transmitting medium in the pressure pipe will generate additional pressure due to the height difference, which will introduce additional errors, thus affecting the measurement accuracy. In the application of industrial processes, since the density of the measured medium is often large, even with a small height difference, the additional error introduced is large.
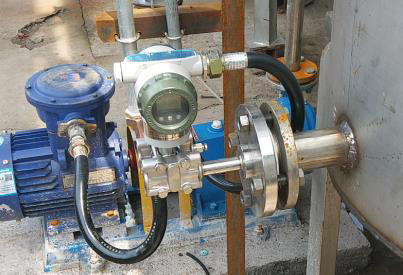
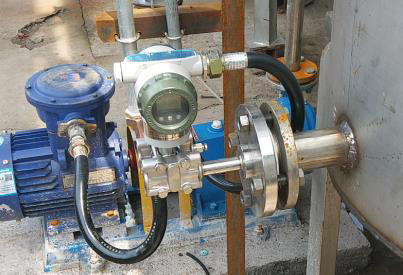
In the use of the pressure sensor, some factors will easily cause malfunction or failing to the sensor if these factors are not be avoided. This article summarizes six factors that are prone to pressure sensor failures, helping users solve malfunction and avoid malfunction in a timely manner.
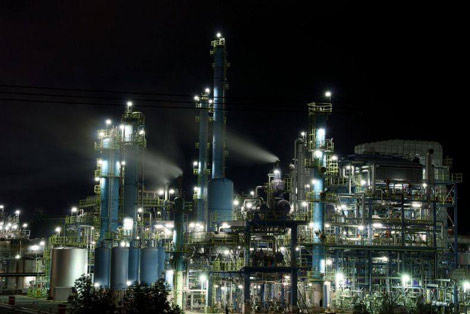
There are 10 types of measurement methods for pressure sensors under most application conditions. The method used for the pressure sensor in measurement is very important to the entire inspection system, which will directly affect whether the measurement task can be completed successfully. In this regard, it is necessary to analyze the different measurement purposes and specific conditions to find a practical way.