Protecting Pressure Sensor from Freezing
In the winter, it is especially important to protect pressure sensors from freezing. When the measured medium is transmitted to the pressure sensor through the measuring pipeline, due to the low ambient temperature, freezing, solidification, and precipitation of crystals often occur, resulting in damage to key parts of the sensor. Exceeding the normal operating temperature range of the sensor due to the low ambient temperature directly affects the accuracy of the sensor indication. Therefore, we must take anti-freezing means to the sensor. So, how do we use the pressure sensor correctly under low temperature conditions?
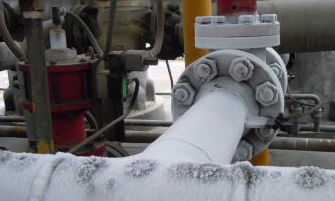
I. Pressure sensor selection: Under freezing conditions, beware of overload pressure
Freezing will affects the function of the sensor. For example, if we drill natural gas in the Arctic, water will also appear in the natural gas pipeline. When the water freezes, the pressure on the pressure sensor may exceed its load range and cause the diaphragm to rupture. If the sensor freezes, we should strictly monitor the corresponding overload pressure.
When measuring with the piezoresistive pressure sensor, the pressure acts indirectly on the silicon diaphragm through the measured medium. The silicon wafer is usually composed of silicone oil. When the temperature drops, the viscosity of the silicone oil decreases. It can gel or even harden. This change will also affect the function of the pressure sensor.
We also need to consider the resistance to condensation: if there is moist air in the housing of the pressure sensor, condensation can form in cold ambient temperatures, which will damage the electronic components and damage the sensor.
When using a pressure sensor at low temperatures, it should be ensured that individual parts could be fused without O-rings and could resistant condensation. In addition, it is also need to estimate whether the pressure sensor will freeze when it comes into contacting with water. In this case, we should select a pressure sensor with a corresponding overload pressure. As with any other application, the pressure sensor should be compensated for the expected temperature range.
II. Heat Tracing for pressure sensor
When use the heat tracing to heat preservation for the pressure sensor, it generally includes two types: steam heat tracing and electric heat tracing. Steam heat tracing is a method that keeping the pressure sensor warm by binding a pipe and injecting heat such as steam. When using this method, pay attention to the length of the pipe, not too long or too short. After the construction is completed, it must be tested for pressure test before it can be used for formal instrument insulation. In the winter, pipelines and temperatures need to be inspected and controlled regularly. Electric heat tracing refers to the use of electric energy to supplement the heat lost by the heating body in the process flow, thereby maintaining the most reasonable process temperature of the flowing medium, and finally achieving the effect of heat preservation for the pressure sensor.
III. Set incubator for pressure sensor
Setting the incubator refers to the process of wrapping the pressure sensor with the incubator and then controlling the temperature through the insulation element in the incubator. One point to note in this process is that the power supply must be properly controlled to ensure that the temperature inside the incubator is appropriate.
IV. Use heating cable for pressure sensor
This is a common way to insulate pressure sensors. Its working principle is to wrap the cable around the shell of the pressure sensor and then energize it. When the current is converted into heat, it achieves the insulation for the pressure sensor.
V. Pressure sensor maintenance
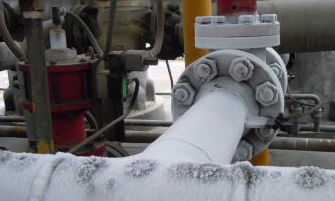
Freezing will affects the function of the sensor. For example, if we drill natural gas in the Arctic, water will also appear in the natural gas pipeline. When the water freezes, the pressure on the pressure sensor may exceed its load range and cause the diaphragm to rupture. If the sensor freezes, we should strictly monitor the corresponding overload pressure.
When measuring with the piezoresistive pressure sensor, the pressure acts indirectly on the silicon diaphragm through the measured medium. The silicon wafer is usually composed of silicone oil. When the temperature drops, the viscosity of the silicone oil decreases. It can gel or even harden. This change will also affect the function of the pressure sensor.
We also need to consider the resistance to condensation: if there is moist air in the housing of the pressure sensor, condensation can form in cold ambient temperatures, which will damage the electronic components and damage the sensor.
When using a pressure sensor at low temperatures, it should be ensured that individual parts could be fused without O-rings and could resistant condensation. In addition, it is also need to estimate whether the pressure sensor will freeze when it comes into contacting with water. In this case, we should select a pressure sensor with a corresponding overload pressure. As with any other application, the pressure sensor should be compensated for the expected temperature range.
II. Heat Tracing for pressure sensor
When use the heat tracing to heat preservation for the pressure sensor, it generally includes two types: steam heat tracing and electric heat tracing. Steam heat tracing is a method that keeping the pressure sensor warm by binding a pipe and injecting heat such as steam. When using this method, pay attention to the length of the pipe, not too long or too short. After the construction is completed, it must be tested for pressure test before it can be used for formal instrument insulation. In the winter, pipelines and temperatures need to be inspected and controlled regularly. Electric heat tracing refers to the use of electric energy to supplement the heat lost by the heating body in the process flow, thereby maintaining the most reasonable process temperature of the flowing medium, and finally achieving the effect of heat preservation for the pressure sensor.
III. Set incubator for pressure sensor
Setting the incubator refers to the process of wrapping the pressure sensor with the incubator and then controlling the temperature through the insulation element in the incubator. One point to note in this process is that the power supply must be properly controlled to ensure that the temperature inside the incubator is appropriate.
IV. Use heating cable for pressure sensor
This is a common way to insulate pressure sensors. Its working principle is to wrap the cable around the shell of the pressure sensor and then energize it. When the current is converted into heat, it achieves the insulation for the pressure sensor.
V. Pressure sensor maintenance
- Installation: Choose a position that is dry and no rain or snow drip for installation.
- Check: If conditions permit, carry out technical confirmation and technical disposal daily on whether the insulation material is damaged and whether the steam pipeline is blocked. During the inspection, it is necessary to check whether the valves of the insulated pipeline, incubators, water traps, electric heating supply components, etc. are normal and the packaging of the insulation materials is intact. Focus on the instrument that is easy to freeze and record it. Dry, complete and clean maintenance of the sensor to solve the problem of heat preservation and heat generation in the field.
- Alarm: if it is possible, we can install a sound and light alarm device, which will alert in the state of steam leakage or power failure, in order to timely find and rectify hidden dangers in insulation and anti-freezing.