Pressure Transducer Response Time/Overload/Vibration/Pipeline
Nowadays, the performance of pressure transducers has increased to the level of solutions available for demanding applications. This article describes the six characteristics and conditions that must be considered when selecting a pressure transducer for measuring differential pressure and critical pressure applications.
The need for fast response times depends on the application. For example, in a wind tunnel application that measures the change in velocity of a dynamic airflow, the signal output of the pressure transducer must vary with wind speed, thus requiring fast response times. For most test benches, leak detection and wind tunnel applications, a response time of 10-80 milliseconds is usually acceptable. For conventional processing and monitoring applications where response time is less important, the response time is typically a few seconds instead of a few milliseconds. When designing a system, it is important to understand the response time requirements of the pressure transducer, not always as fast as possible. If the pressure transducer response is too fast, sometimes the transducer will respond to brief, unfiltered and unwanted system noise or turbulent pressure fluctuations. In this case, filtering the output signal can attenuate these unnecessary interferences.
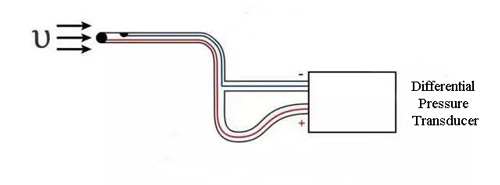
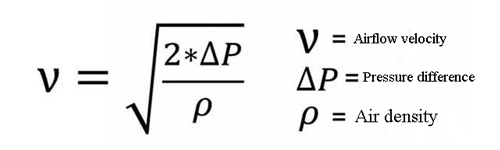
The latest generation of pressure transducers must address these issues. Therefore, the pressure transducer becomes more robust. They can withstand relatively higher overload, either positive (process) or negative (reference). This is a very important new feature. Previously, pressure transducers only had overload protection in the positive direction. However, a reverse leak will result in a reverse overload to the pressure transducer. Pressure transducers that are fully protected in both directions are suitable for applications where accidental overload or large leaks may occur. If it happens, the pressure transducer will continue to work normally.
The pressure transducer can withstand unexpected overloads other than its rated withstand pressure (such as 150 PSI) and then return to normal. If the withstand pressure is exceeded, the diaphragm will be permanently deformed, causing a zero drift. If the pressure at any of the ports exceeds the burst pressure (such as 300 PSI), the pressure transducer's measurement chamber will be destroyed, causing weld failure, seal leakage, or rupture of the diaphragm or casing. The user must be aware of the pressure transducer's withstand pressure and burst pressure limits. In addition, the user must understand that the system may be accidentally ventilated or that the components of the test equipment are not sealed, which will damage the pressure transducer. Therefore, users should avoid these unexpected situations by using a stainless steel pressure transducer that is small, sturdy and has sufficient overload protection in both directions.
Fortunately, the measurement error caused by pipeline pressure can be corrected by recalibration or re-zeroing for the pressure transducer. It can be done manually with a potentiometer, or it can be easily and safely adjusted using an advanced model with a small calibration button (equipped with a digital display mounted on the transducer). Calibration key functions include zero point, range reset, and factory reset.
Finally, look for a supplier of pressure transducers that supply a variety of configurations for pressure transducer. It will enable end users to work with a manufacturer to obtain a pressure transducers with specific accuracy, output signals and ranges for a variety of different applications.
- Response time of the pressure transducer
The need for fast response times depends on the application. For example, in a wind tunnel application that measures the change in velocity of a dynamic airflow, the signal output of the pressure transducer must vary with wind speed, thus requiring fast response times. For most test benches, leak detection and wind tunnel applications, a response time of 10-80 milliseconds is usually acceptable. For conventional processing and monitoring applications where response time is less important, the response time is typically a few seconds instead of a few milliseconds. When designing a system, it is important to understand the response time requirements of the pressure transducer, not always as fast as possible. If the pressure transducer response is too fast, sometimes the transducer will respond to brief, unfiltered and unwanted system noise or turbulent pressure fluctuations. In this case, filtering the output signal can attenuate these unnecessary interferences.
- Overload protection of the pressure transducer
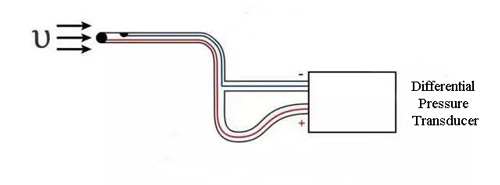
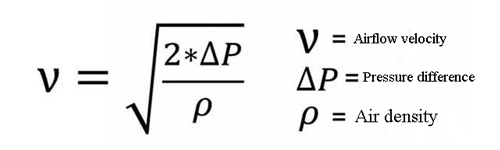
- Overload protection of the pressure transducer
The latest generation of pressure transducers must address these issues. Therefore, the pressure transducer becomes more robust. They can withstand relatively higher overload, either positive (process) or negative (reference). This is a very important new feature. Previously, pressure transducers only had overload protection in the positive direction. However, a reverse leak will result in a reverse overload to the pressure transducer. Pressure transducers that are fully protected in both directions are suitable for applications where accidental overload or large leaks may occur. If it happens, the pressure transducer will continue to work normally.
The pressure transducer can withstand unexpected overloads other than its rated withstand pressure (such as 150 PSI) and then return to normal. If the withstand pressure is exceeded, the diaphragm will be permanently deformed, causing a zero drift. If the pressure at any of the ports exceeds the burst pressure (such as 300 PSI), the pressure transducer's measurement chamber will be destroyed, causing weld failure, seal leakage, or rupture of the diaphragm or casing. The user must be aware of the pressure transducer's withstand pressure and burst pressure limits. In addition, the user must understand that the system may be accidentally ventilated or that the components of the test equipment are not sealed, which will damage the pressure transducer. Therefore, users should avoid these unexpected situations by using a stainless steel pressure transducer that is small, sturdy and has sufficient overload protection in both directions.
- Vibration of the pressure transducer
- Effect to pipeline pressure of the pressure transducer
Fortunately, the measurement error caused by pipeline pressure can be corrected by recalibration or re-zeroing for the pressure transducer. It can be done manually with a potentiometer, or it can be easily and safely adjusted using an advanced model with a small calibration button (equipped with a digital display mounted on the transducer). Calibration key functions include zero point, range reset, and factory reset.
- Other considerations
Finally, look for a supplier of pressure transducers that supply a variety of configurations for pressure transducer. It will enable end users to work with a manufacturer to obtain a pressure transducers with specific accuracy, output signals and ranges for a variety of different applications.