How to Use Differential Pressure Sensor
Differential pressure sensor is a kind of instrument widely used in industrial production. It can measure many physical parameters. The pressure of gas and liquid can obtained by differential pressure sensor, which is of great significance for industrial production.
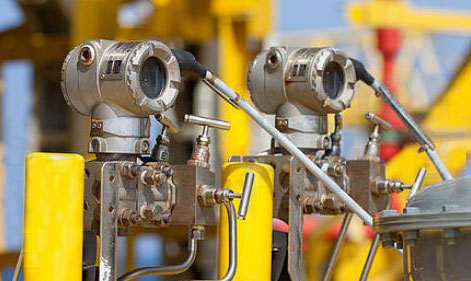
The differential pressure sensor usually used with orifice flowmeters, V-cone flowmeters, elbow flowmeters, Verabar flowmeters, and Annubar (both beam tube) flowmeters together to measure the industrial flow, whose effect is very significant.
As the detection and transformation part of the process control system, the differential pressure sensor converts the process parameters such as differential pressure, flow rate and liquid level of liquid, gas or steam into a unified standard signal (such as DC 4-20mA current) . The signal as a input signal of the display instrument, operator and regulator for continuous detection and automatic control of the production process
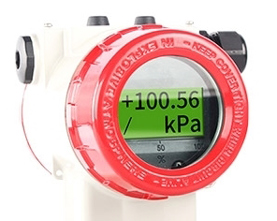
III. When measuring the gas flow rate, the differential pressure sensor should be installed beside or above the tested pipe in order to easily flow accumulated liquid into the pipe.
IV. When measuring the steam flow, the differential pressure sensor should be installed below the tested pipe to fill the condensate in the pressure pipe. In addition, when measuring steam or other high temperature media, we must pay attention to prevent the temperature of the differential pressure sensor from contacting the medium beyond the limit temperature specified by the sensor.
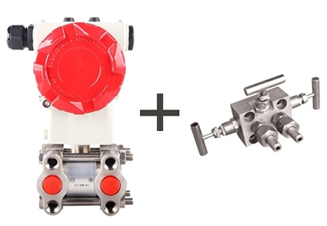
Open the balance valve and close the two shut-off valves, then we can zero check the sensor.
III. Precautions when zeroing for the differential pressure sensor

6.2 Before starting to use, if the valve is closed, the valve should be opened very carefully and slowly, so as to prevent the measured medium from directly impacting the sensor diaphragm, thus damaging the sensor diaphragm.
6.3 The pipe must remain unblocked because deposits in the pipe will pop up and damage the sensor diaphragm.
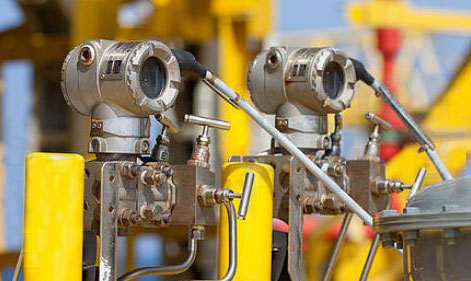
As the detection and transformation part of the process control system, the differential pressure sensor converts the process parameters such as differential pressure, flow rate and liquid level of liquid, gas or steam into a unified standard signal (such as DC 4-20mA current) . The signal as a input signal of the display instrument, operator and regulator for continuous detection and automatic control of the production process
- Wiring procedure for the differential pressure sensor
- Remove the electronic housing.
- Connect the positive lead to the “PWR/COMN” terminal and the negative lead to the “-” terminal. Be careful not to connect the live signal line to the test terminal (Test) because powering up will damage the test diode in the test circuit. Use shielded twisted pair for best measurement results. To ensure proper communication, we should use a 24AWG or higher cable.
- Seal the unused conduit interface on the sensor housing with a conduit plug.
- Re-screw the cover
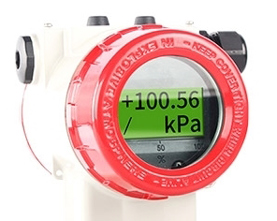
- Installation requirements of the differential pressure sensor
- Prevent the sensor from coming into direct contact with corrosive or overheated measured medium;
- Prevent dross from depositing and clogging in the pressure tube;
- The length of the pressure tube on both sides of the positive and negative pressure should be as equal as possible;
- The liquid column indenter in the pressure tube on both sides of the positive and negative pressure should be balanced;
-
Install the pressure tube at the position where the temperature gradient and temperature fluctuations are minimal.
III. When measuring the gas flow rate, the differential pressure sensor should be installed beside or above the tested pipe in order to easily flow accumulated liquid into the pipe.
IV. When measuring the steam flow, the differential pressure sensor should be installed below the tested pipe to fill the condensate in the pressure pipe. In addition, when measuring steam or other high temperature media, we must pay attention to prevent the temperature of the differential pressure sensor from contacting the medium beyond the limit temperature specified by the sensor.
- Put into operation and zero check
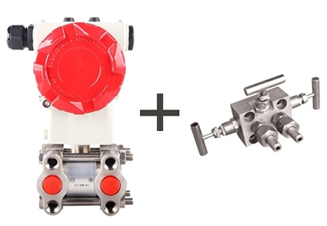
- Open the two drain valves on the differential pressure sensor;
- Open the balance valve;
- Slowly open the two shut-off valves to remove air or dirt from the pressure guiding tube;
- Close the two drain valves;
- Close the balance valve and the sensor is ready for operation.
Open the balance valve and close the two shut-off valves, then we can zero check the sensor.
III. Precautions when zeroing for the differential pressure sensor
- Don't confuse zero adjustment screw and span adjustment screw. Do not adjust the range of the differential pressure sensor at the installation site.
- When the differential pressure sensor is zeroing, the temperature of the positive and negative pressure chambers and the pressure pipe on both sides must be the same. If there is a temperature difference between the two sides, the adjusted zero point will drift with time.
- If used the sensor for positive and negative migration compensation in the field, the zero adjustment should be made in the commissioning state. If the migration amount is too large, the migration compensation can no longer perform on the differential pressure sensor.

- Precautions in daily use
- Do not apply a voltage higher than 36V to the sensor, otherwise the sensor will be damaged.
- Do not touch the diaphragm with a hard object, as this will cause the isolation diaphragm damage.
- The measured medium cannot freeze, otherwise it will damage the components and the isolation diaphragm, causing the sensor damage. If it is necessary, temperature protection of the sensor to prevent icing is need to do.
- When measuring steam or other high temperature media, the temperature should not exceed the limit temperature of the sensor when used. Above the limit temperature used by the sensor, we must use a heat sink.
- When measuring steam or other high temperature media, use a heat pipe to connect the sensor with the pipe and transfer the pressure on the pipe to the transformer. When the measured medium is water vapor, inject an appropriate amount of water into the heat pipe to prevent the superheated steam from directly contacting the sensor, damaging the sensor.
- In the process of pressure transmission, please note the following points.
6.2 Before starting to use, if the valve is closed, the valve should be opened very carefully and slowly, so as to prevent the measured medium from directly impacting the sensor diaphragm, thus damaging the sensor diaphragm.
6.3 The pipe must remain unblocked because deposits in the pipe will pop up and damage the sensor diaphragm.
- Summarize