How to Maintain Differential Pressure Sensor in Daily Use
The differential pressure sensor has strict requirements in the daily use and maintenance. Only follow the standard installation and maintenance requirements, the differential pressure sensor can operate normally. This article describes the six items that need to be paid attention to in the application of differential pressure sensors to help users use the products correctly.
1. Choose the right installation position
When the differential pressure sensor is installed too close to the upstream of the production line, the unmelted material will wear the top of the sensor. If the sensor is installed in a position that is too far behind, a stagnant zone of molten material will be created between the sensor and the screw stroke, in which the melt is likely to be degraded, and the pressure signal may also transmit distortionally. In general, the sensor can be located on the barrel in front of the screen, in front of or behind the melt pump, or in the mold.
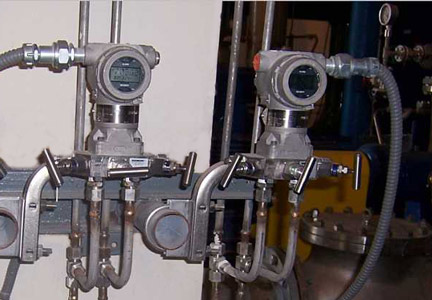
2. Check the size of the mounting hole size
If the size of the mounting hole is not suitable, the threaded portion of the differential pressure sensor is more susceptible to certain wear during installation. This will not only directly affect the sealing of the equipment, but also make the pressure sensor not fully functioning, and may even pose a safety hazard. Only use suitable mounting holes to avoid thread abrasion. Usually we can perform a fine inspection for the mounting holes with a mounting hole measuring instrument to make the appropriate adjustments.
3. Avoid low temperature interference
In the extrusion process, if the extruder does not reach the operating temperature before starting production, the sensor and extruder will be damaged with some extent. In addition, if the sensor is removed from the cold extruder, the material may stick to the top of the sensor causing damage to the vibration diaphragm. Therefore, before removing the differential pressure sensor, we should confirm that the temperature of the barrel is sufficiently high and the material inside the barrel is in a softened state.
4. Keep dry
Although the circuit design of the differential pressure sensor can withstand the harsh extrusion processing environment, some sensors are not waterproof, and the humid environment is not conducive to the normal operation of the sensor. Therefore, it is necessary to ensure that the water in the water-cooling device of the barrel in the extruder does not leak, otherwise the sensor may be adversely affected. If the sensor must exposed to water or wet environment, choose a special sensor with extremely waterproof.
5. Keep the mounting holes clean
Keeping the mounting holes clean is mainly to prevent clogging of the melt, which is extremely important to ensure the normal operation of the equipment. All pressure sensors on the barrel should be removed to avoid damage before cleaning the extruder. When removing the sensor, the melt may flow into the mounting hole and harden. If the residual melt is not removed, the top of the sensor may be damaged when the sensor is installed again. The cleaning kit can remove these melt residues. However, repeated cleaning processes may deepen the damage to the sensor caused by the mounting holes. If this happens, we should take measures to raise the position of the sensor in the mounting hole.
6. Serious and comprehensive cleaning
All differential pressure sensors should be removed before cleaning the barrel of the extruder with a wire brush or special compound. Because both methods of cleaning will cause damage to the vibration diaphragm of the sensor. When heating the barrel, the sensor should also be removed and wipe it with a soft cloth that does not cause wear, and clean the sensor holes with a drill and guide sleeve.
1. Choose the right installation position
When the differential pressure sensor is installed too close to the upstream of the production line, the unmelted material will wear the top of the sensor. If the sensor is installed in a position that is too far behind, a stagnant zone of molten material will be created between the sensor and the screw stroke, in which the melt is likely to be degraded, and the pressure signal may also transmit distortionally. In general, the sensor can be located on the barrel in front of the screen, in front of or behind the melt pump, or in the mold.
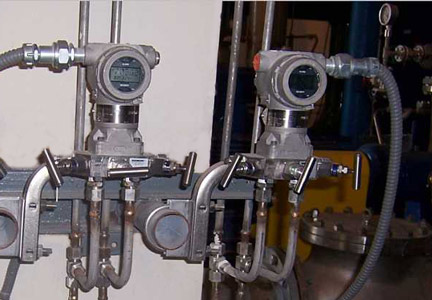
2. Check the size of the mounting hole size
If the size of the mounting hole is not suitable, the threaded portion of the differential pressure sensor is more susceptible to certain wear during installation. This will not only directly affect the sealing of the equipment, but also make the pressure sensor not fully functioning, and may even pose a safety hazard. Only use suitable mounting holes to avoid thread abrasion. Usually we can perform a fine inspection for the mounting holes with a mounting hole measuring instrument to make the appropriate adjustments.
3. Avoid low temperature interference
In the extrusion process, if the extruder does not reach the operating temperature before starting production, the sensor and extruder will be damaged with some extent. In addition, if the sensor is removed from the cold extruder, the material may stick to the top of the sensor causing damage to the vibration diaphragm. Therefore, before removing the differential pressure sensor, we should confirm that the temperature of the barrel is sufficiently high and the material inside the barrel is in a softened state.
4. Keep dry
Although the circuit design of the differential pressure sensor can withstand the harsh extrusion processing environment, some sensors are not waterproof, and the humid environment is not conducive to the normal operation of the sensor. Therefore, it is necessary to ensure that the water in the water-cooling device of the barrel in the extruder does not leak, otherwise the sensor may be adversely affected. If the sensor must exposed to water or wet environment, choose a special sensor with extremely waterproof.
5. Keep the mounting holes clean
Keeping the mounting holes clean is mainly to prevent clogging of the melt, which is extremely important to ensure the normal operation of the equipment. All pressure sensors on the barrel should be removed to avoid damage before cleaning the extruder. When removing the sensor, the melt may flow into the mounting hole and harden. If the residual melt is not removed, the top of the sensor may be damaged when the sensor is installed again. The cleaning kit can remove these melt residues. However, repeated cleaning processes may deepen the damage to the sensor caused by the mounting holes. If this happens, we should take measures to raise the position of the sensor in the mounting hole.
6. Serious and comprehensive cleaning
All differential pressure sensors should be removed before cleaning the barrel of the extruder with a wire brush or special compound. Because both methods of cleaning will cause damage to the vibration diaphragm of the sensor. When heating the barrel, the sensor should also be removed and wipe it with a soft cloth that does not cause wear, and clean the sensor holes with a drill and guide sleeve.