How to Calibrate Pressure Transducer
This article describes how to calibrate piezoresistive pressure transmitters and differential pressure transmitters. The calibration process includes preparation work, equipment connection, and pre-boost. In addition, this paper also introduces the problems that may occur in the pressure transducer and differential pressure transducer during the calibration process and the corresponding solutions.
If there is any residual liquid in the pipeline, it should be discharged in time and then checked. At the same time, it is necessary to avoid checking the upper stroke without checking the downstroke in order to increase the speed during the calibration process.
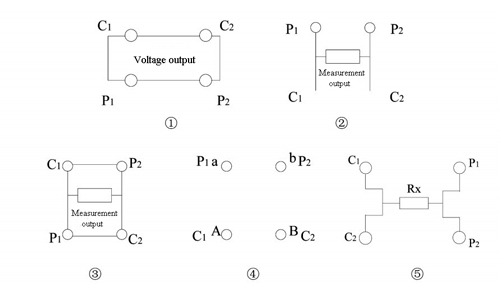
- Preparation before pressure transducer calibration
- Connect the pressure guiding tube correctly and fix the calibrated pressure transducer
- Connect the signal cable of the pressure transducer correctly
- Pre-boost the pressure transducer. Detect its tightness
- Drain the residual liquid inside the differential pressure transducer with a three valves mainfold.
- Detect the tightness of the entire system. If it is found a leak, you can use the sound to confirm the most easily leaked parts. If the fault persists, the easiest way is to put the measured object in the basin to see the bubbles, but pay attention to the depth.
- Fill the conduit with pressure transmitting medium to cause the pressure system to operate normally to formally verify the pre-boost.
- Possible problems in the calibration process of the pressure transducer and corresponding solutions
- Laboratory windowing or air conditioning causes excessive airflow, which affects the stability of the input. The pressure of human body blowing is about 700Pa, and special attention should be paid to the pressure within 5kPa. The test bench can be placed in an area where the air flow is relatively stable to reduce measurement errors.
- If there is residual liquid or sediment or other foreign matter flowing into the pressure guiding pipe in the pressure pipe, measurement errors will occur, and it should be removed in time. For a differential pressure transducer with the three valves manifold, it can press the upper limit of the range and then open the balancing valve, and the residual liquid will flow out from the L end.
- The boost is not stable. The pressure signal should be input smoothly to each calibration point during the calibration process. It should be slow enough to approach the calibration point to avoid overshoot.
If there is any residual liquid in the pipeline, it should be discharged in time and then checked. At the same time, it is necessary to avoid checking the upper stroke without checking the downstroke in order to increase the speed during the calibration process.
- Before the test, warm up the standard device and turn on the calibrated differential pressure transducer. After the connection is stabilized, the line is connected and tested.
- Distinguish whether the grounding resistance tester is a DC output or an AC output. Select the appropriate button on the standard. If the selection is wrong, it is prone to no output current display and no change in resistance.
- In the calibration process, the selection of the resistance value is uniformly selected according to the range of 20% to 100% of the range. Unless otherwise specified, in actual detection, 10A and 25A are generally used as the basic current range.
- In the calibration of the grounding on-resistance alarm preset error, the regulation stipulates that the adjustable standard resistor method or the standard voltage source method can be used. For the standard voltage source method, it is generally not easy to operate, and it is easy to produce operational errors. As mentioned earlier, the standard resistor method should be used in the detection of the arbitrated resistance indication error. This shows that the application of the standard resistor method is reliable relative to the standard voltage source method. Therefore, when performing alarm preset error, it is advisable to select the standard resistor method.
- After the grounding on-resistance tester has been tested, the grounding on-resistance tester should be turned off, and then the standard is turned off to avoid current short circuit in the tester.
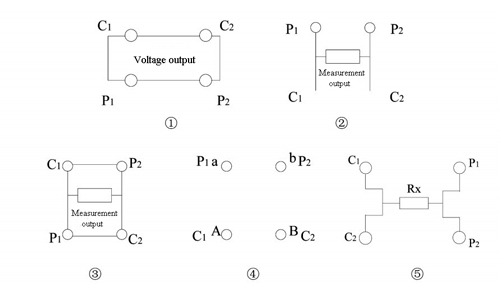