Gas and Air Pressure Sensor Working Principle and Applications
The gas or air pressure sensor is a conversion device mainly used to measure the absolute pressure of the gas. The gas pressure sensor is based on air pressure as a conducted object, which is a control sensor that realizes induction control.
Inside the gas pressure sensor, there is an intake pipe that allowing air to enter the sensor. Once energized, the air can be connected to the inside of the pressure sensor. When the gas enters, the pressure that squeeze the sensor is generated. By capturing the amount of current inside the circuit, it is possible to transmit electronic signals simply by the magnitude of the pressure. Thereby, a working signal is sent to the device controlled by the gas pressure sensor to make it move and complete a whole set of work.
A gas pressure sensor is a device that converts a specific measured pressure into a certain available signal output according to a certain rule. It can meet the requirements of information transmission, processing, recording, display and manipulation. Therefore, gas pressure sensors are widely used in environmental monitoring as an effective and fast inspection tool. As a major means of environmental protection, environmental monitoring provides a basis for environmental management, planning and scientific research by reflecting the current status and development trends of environmental quality in a timely, accurate and comprehensive manner.
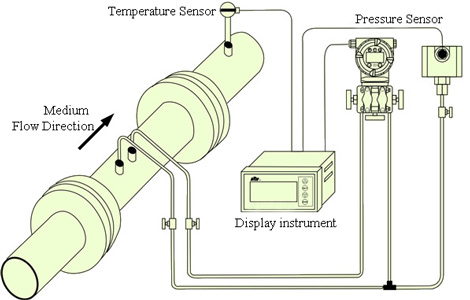
With the increasing international environmental control, the use of gas inspection instruments for environmental protection has also increased year by year. For example, gas pressure sensors for checking automobile exhaust, factory exhaust, flue gas, indoor air, etc.
The development of electronic technology, biotechnology and optical technology has also promoted the research of gas pressure sensors. These technologies are gradually being applied to the research and development of gas sensors, such as carbon nanotubes, gold nanoparticles, and biological antibody antigen properties. Therefore, in various types of gas inspection equipment, gas pressure sensors occupy a very important position, which also plays a role in energy conservation and environmental protection.
For high temperature gas pressure sensors, the temperature of the measured medium should be maintained within the temperature range in which the sensor can operate normally. If the temperature is outside the applicable range, the error will become very large and life of the instrument will be shortened accordingly. High temperature gas pressure sensor will measure and compensate for temperature effects during production. It can ensure that the measurement error caused by temperature effects within the accuracy requirements. In the case with high temperature, it is conceivable to select a high temperature gas pressure sensor or install condensers and radiators to assist in cooling.
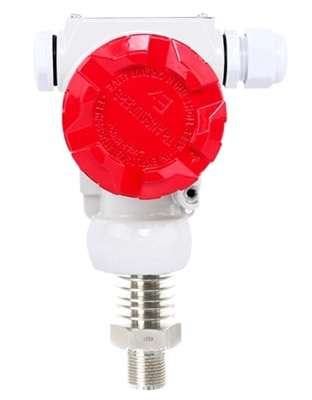
The uncertainty of the use in a high temperature gas pressure sensor is reflected in whether the change in its indication is caused by pressure change or by temperature change. Temperature effects are the most complex part when understanding how to use high temperature gas pressure sensors. In addition to the need to control the temperature in the measurement site, the use of high temperature gas pressure sensors also requires attention to many problems.
High temperature pressure sensor is a high accuracy and high stability pressure sensor, whose core component is high temperature pressure resistant core. The sensor convert the measured pressure into 4-20mA, 0-20mA, 0-5V, 1-5V, 0-10V, RS485 and other standard electrical signals through high-reliability amplifier circuit and precise temperature compensation. It can be used in pressure measurement for high temperature gas, water and oil. The hermetically sealed package technology and the complete assembly process ensure excellent quality and performance. The pressure sensor has a variety of thread connections and a variety of lead methods to meet customer needs. It is suitable for use with various measurement and control equipment in high temperature industrial environments and can be used in wet and harsh environments for a long time.
An air compressor is a device that uses an electric motor to compress a gas in a compression chamber to give it a certain pressure. As a basic industrial equipment, air compressors are widely used in metallurgy, machinery manufacturing, mining, power, petrochemical, textile and other industries. Its electricity consumption accounts for 15% of the power consumption in general industrial equipment. Therefore, it has economic and social benefits for energy-saving renovation.
The principle of frequency conversion and energy saving is summarized as follows. First, the gas pressure sensor measure the pipe network pressure. The measured value is compared with the set value of the pressure by the PID regulator to obtain a deviation value. This deviation value is directly used as the given frequency value of the inverter. The alternating current with corresponding frequency response and voltage amplitude output from the frequency converter. Then the corresponding speed on the motor is get. The air compressor outputs the corresponding compressed air to the air tank to change its pressure. This change continues until the pipe network pressure is the same as the given pressure value.
- Working principle of the gas pressure sensor
Inside the gas pressure sensor, there is an intake pipe that allowing air to enter the sensor. Once energized, the air can be connected to the inside of the pressure sensor. When the gas enters, the pressure that squeeze the sensor is generated. By capturing the amount of current inside the circuit, it is possible to transmit electronic signals simply by the magnitude of the pressure. Thereby, a working signal is sent to the device controlled by the gas pressure sensor to make it move and complete a whole set of work.
- Applications of the gas pressure sensor
A gas pressure sensor is a device that converts a specific measured pressure into a certain available signal output according to a certain rule. It can meet the requirements of information transmission, processing, recording, display and manipulation. Therefore, gas pressure sensors are widely used in environmental monitoring as an effective and fast inspection tool. As a major means of environmental protection, environmental monitoring provides a basis for environmental management, planning and scientific research by reflecting the current status and development trends of environmental quality in a timely, accurate and comprehensive manner.
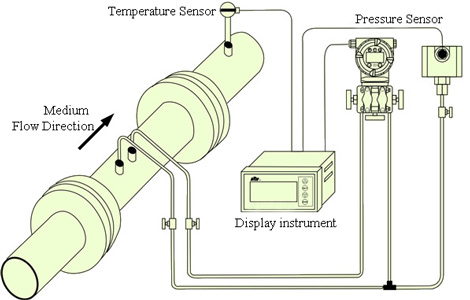
With the increasing international environmental control, the use of gas inspection instruments for environmental protection has also increased year by year. For example, gas pressure sensors for checking automobile exhaust, factory exhaust, flue gas, indoor air, etc.
The development of electronic technology, biotechnology and optical technology has also promoted the research of gas pressure sensors. These technologies are gradually being applied to the research and development of gas sensors, such as carbon nanotubes, gold nanoparticles, and biological antibody antigen properties. Therefore, in various types of gas inspection equipment, gas pressure sensors occupy a very important position, which also plays a role in energy conservation and environmental protection.
- What is a high temperature gas pressure sensor
For high temperature gas pressure sensors, the temperature of the measured medium should be maintained within the temperature range in which the sensor can operate normally. If the temperature is outside the applicable range, the error will become very large and life of the instrument will be shortened accordingly. High temperature gas pressure sensor will measure and compensate for temperature effects during production. It can ensure that the measurement error caused by temperature effects within the accuracy requirements. In the case with high temperature, it is conceivable to select a high temperature gas pressure sensor or install condensers and radiators to assist in cooling.
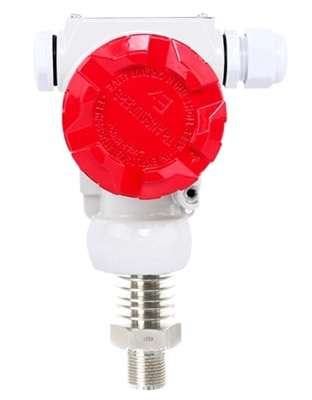
The uncertainty of the use in a high temperature gas pressure sensor is reflected in whether the change in its indication is caused by pressure change or by temperature change. Temperature effects are the most complex part when understanding how to use high temperature gas pressure sensors. In addition to the need to control the temperature in the measurement site, the use of high temperature gas pressure sensors also requires attention to many problems.
High temperature pressure sensor is a high accuracy and high stability pressure sensor, whose core component is high temperature pressure resistant core. The sensor convert the measured pressure into 4-20mA, 0-20mA, 0-5V, 1-5V, 0-10V, RS485 and other standard electrical signals through high-reliability amplifier circuit and precise temperature compensation. It can be used in pressure measurement for high temperature gas, water and oil. The hermetically sealed package technology and the complete assembly process ensure excellent quality and performance. The pressure sensor has a variety of thread connections and a variety of lead methods to meet customer needs. It is suitable for use with various measurement and control equipment in high temperature industrial environments and can be used in wet and harsh environments for a long time.
- Application of gas pressure sensor in air compressor
An air compressor is a device that uses an electric motor to compress a gas in a compression chamber to give it a certain pressure. As a basic industrial equipment, air compressors are widely used in metallurgy, machinery manufacturing, mining, power, petrochemical, textile and other industries. Its electricity consumption accounts for 15% of the power consumption in general industrial equipment. Therefore, it has economic and social benefits for energy-saving renovation.
The principle of frequency conversion and energy saving is summarized as follows. First, the gas pressure sensor measure the pipe network pressure. The measured value is compared with the set value of the pressure by the PID regulator to obtain a deviation value. This deviation value is directly used as the given frequency value of the inverter. The alternating current with corresponding frequency response and voltage amplitude output from the frequency converter. Then the corresponding speed on the motor is get. The air compressor outputs the corresponding compressed air to the air tank to change its pressure. This change continues until the pipe network pressure is the same as the given pressure value.