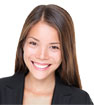
Pressure Sensor
Home » Application » Page 3
Pressure sensors are mainly used in pressure measurement for hydraulic and gas. In the hydraulic system, the closed-loop control of force is mainly the action of the pressure sensor. Many physical and chemical properties, such as point, boiling point, vapor pressure, etc., are almost related to pressure. Gas pressure measurement is of great significance.
Nowadays, the performance of pressure transducers has increased to the level of solutions available for demanding applications. This article describes the six characteristics and conditions that must be considered when selecting a pressure transducer for measuring differential pressure and critical pressure applications.
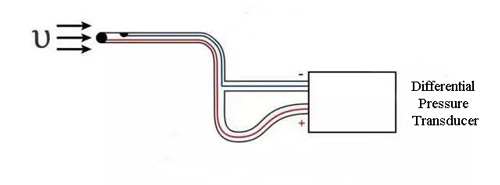
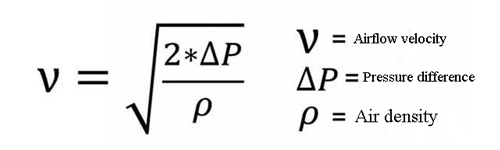
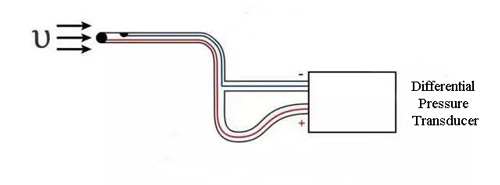
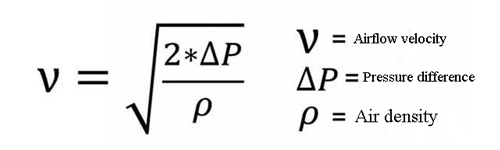
This paper introduces the pressure sensor selection for nuclear power plant application. Combined with the technical requirements to pressure sensors for nuclear power plants, the paper gives the selection methods and precautions to provide reference for the selection and design of pressure sensors to nuclear power plants.
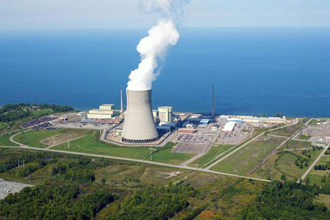
For nuclear power plants, the process detection instrument is the interface between the entire instrument control system and the process. The performance of the instrument directly affects the performance of the instrument control system. For various process instruments, the pressure sensor is the most wide and common in use. It is mainly used to detect the pressure, flow and liquid level for the process system. Pressure sensors provide the necessary signals for nuclear power plant protection systems and post-accident monitoring systems for safety protection and post-accident monitoring. Therefore, the correct and reasonable selection for pressure sensors is very important to ensure the safe and reliable operation of nuclear power plants.
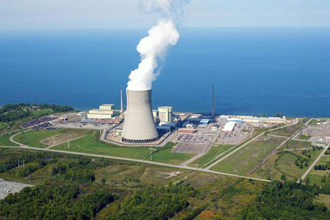
For nuclear power plants, the process detection instrument is the interface between the entire instrument control system and the process. The performance of the instrument directly affects the performance of the instrument control system. For various process instruments, the pressure sensor is the most wide and common in use. It is mainly used to detect the pressure, flow and liquid level for the process system. Pressure sensors provide the necessary signals for nuclear power plant protection systems and post-accident monitoring systems for safety protection and post-accident monitoring. Therefore, the correct and reasonable selection for pressure sensors is very important to ensure the safe and reliable operation of nuclear power plants.
There are many problems to be aware of in pressure sensor connection and Installation. The pressure sensor itself is a strong, durable and reliable electromechanical product, but in order to ensure the measurement accuracy. This article summarizes the issues that should be considered when using pressure sensors.
The function of the pressure sensor is to measure medium pressure such as gas, oil or steam, and then convert the pressure signal into a standard current signal output to supply to secondary instrument such as alarms, recorders, regulators, etc. for measurement, indication and process adjustment. During the use of the pressure sensor, there are often many process parameters are incorrect. For example, the installation of throttling device, condensation tank and pressure guiding tube are not standard, the pressure guiding tube is blocked, electromagnetic interference as well as maintenance, etc. Many of the flow, level and pressure measured by the pressure sensor are involved in the automatic control of the system. Some pressure and differential pressure are also involved in the shutdown control. If the measurement accuracy is not high, it not only affects the accuracy of the automatic control, but also affects the stability of production. These put higher demands on the measurement accuracy and pressure sensor stability.
The pressure sensor current output fluctuation or instability is a failure often encountered in use. This article summarizes the maintenance experience for handling this fault, helping users quickly master the skills in pressure sensor fault repairing.
The pressure sensor output current fluctuation can be clearly seen on the DCS display curve. Therefore, when checking for a fault, we can switch the control system to manual mode to observe the fluctuation. If the measurement curve is still fluctuating frequently, it should be the cause of the process. If the fluctuation is reduced, it possibly be the pressure sensor fault or the PID parameter is improperly set. Sometimes adjusting the damping time of the pressure sensor appropriately can reduce the parameter fluctuation.
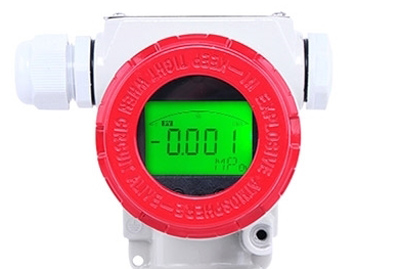
The pressure sensor output current fluctuation can be clearly seen on the DCS display curve. Therefore, when checking for a fault, we can switch the control system to manual mode to observe the fluctuation. If the measurement curve is still fluctuating frequently, it should be the cause of the process. If the fluctuation is reduced, it possibly be the pressure sensor fault or the PID parameter is improperly set. Sometimes adjusting the damping time of the pressure sensor appropriately can reduce the parameter fluctuation.
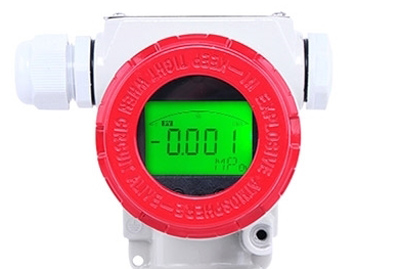
The selection principles for the pressure transducer are different under different application conditions. This article will introduce how to select the pressure transducer in a corrosive, high temperature, high viscosity and easy to crystallize application environment.
During the selection of the pressure sensor, the right specifications are the important thing that must be considered carefully. Different types of pressure sensors vary widely in principle and structure. How to properly select the sensor according to the specific measurement purpose, measurement object and measurement environment is the first problem to be solved before pressure measurement. After the selection of the pressure sensor have determined, the matching measurement method and measurement device can be determined. The success or failure of the measurement result largely depends on whether the sensor selection is reasonable.
The liquid column static pressure will affect the measurement accuracy of the pressure sensor in the actual production process. It is common for the pressure sensor installation below the pressure tapping point. When measuring steam and liquid medium, the output value Pi of the pressure sensor is the sum of the actual working pressure Pg and the liquid column static pressure Ps due to the liquid column static pressure, which produces an additional error. For example, the installation position of the pressure sensor is 10m below the measuring point. If the pressure sensor indication is 5.04MPa, it including the liquid column static pressure value. Therefore, the difference that subtracting the liquid column static pressure value is the actual working pressure value.
In the winter, it is especially important to protect pressure sensors from freezing. When the measured medium is transmitted to the pressure sensor through the measuring pipeline, due to the low ambient temperature, freezing, solidification, and precipitation of crystals often occur, resulting in damage to key parts of the sensor. Exceeding the normal operating temperature range of the sensor due to the low ambient temperature directly affects the accuracy of the sensor indication. Therefore, we must take anti-freezing means to the sensor. So, how do we use the pressure sensor correctly under low temperature conditions?
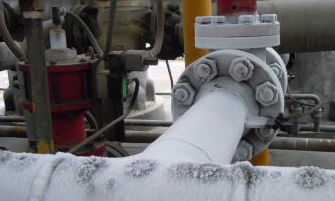
During the daily use of pressure sensors, users often ignore some preventive maintenance work. The pressure sensor and the differential pressure sensor can be remotely operated online through the hand-operated communicator, which greatly facilitates the maintenance of the instrument, so that we don't need to go to the scene to observe the sensor frequently in daily maintenance. In addition, the reliability of this type of instrument is high, so the problem is the neglect of it. It is difficult to find the existence of hidden dangers before the failure occurs. We need to pay attention to the following questions.
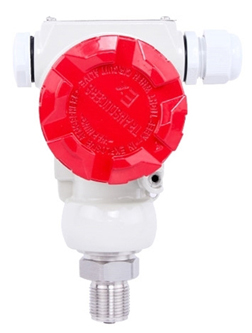
Pressure sensors often occurred in failure during use due to some reasons. The reasons may be the user' s own use method is inappropriate, or the external environmental factors have changed, or the quality of the sensor production is not enough, etc., which may cause the pressure sensor to failure. Here are some of the most common failures and solutions for the pressure sensor, so that everyone can find the problem rapidly.