Air Pressure Sensor Working Principle and Use
The air pressure sensor is a conversion device mainly used for measuring the absolute pressure, gauge pressure and differential pressure of the gas. It is applied to pneumatic control systems and hydraulic systems for pressure measurement of wind pressure and pipeline gas, etc.
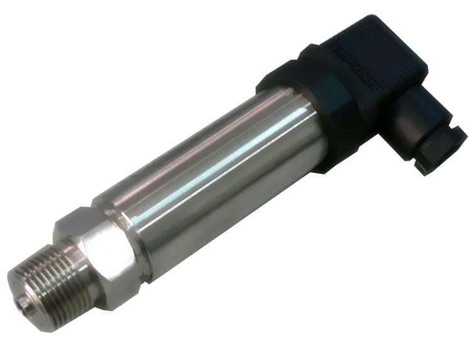
Therefore, the user must pay attention to maintain the pressure sensor during use. Although the pressure sensor has a stainless steel housing, it is still easily damaged. In particular, some improper operations will easily cause damage to the pressure sensor.
1. Using the air pressure sensor over the measuring range
In general, the use of pressure sensors in overrange is the principal cause for sensor damage. Do not apply pressure to the pressure sensor that exceeds the rated withstand pressure. If a pressure higher than the withstand pressure is applied, it is highly likely to cause breakage.
2. Use environment of the air pressure sensor
Second is the use environment of the air pressure sensor. Avoid using pressure sensors in environments with flammable and explosive gases. If pressure measurements are required in high temperature, humidity, and harsh environments, must use special types of pressure sensors to adapt to the changes in environmental conditions.
3. Power supply voltage and load short circuit
The problem of power supply voltage and load short circuit must also be noted. Do not exceed the rated voltage range when using the air pressure sensor. If a voltage exceeding the rated voltage range is applied, the sensor may be broken or burnt. In addition, avoid shorting the load, otherwise it will also cause the pressure sensor to rupture or burn. There is a point that easily be overlooked is incorrect wiring. Avoid incorrect wiring for the polarity of the power supply.
- The air pressure sensor working principle
- There are an intake pipe and a vacuum pipe inside the air pressure sensor. The intake pipe is mainly responsible for the entry of air. When the air enter the inside of the pressure sensor, it will put pressure on the vacuum tube. The value of this pressure will increase as the amount of air entering increases. The other side of the vacuum tube is equipped with a piezoresistive resistor. A piezoresistive resistor is a rheostat that can continuously change the resistance of the resistor based on the pressure value. The magnitude of the resistance value is proportional to the magnitude of the current in the circuit, converting the pressure to a standard current signal. The control functions of the device and circuit can be realized according to different current signals from the pressure sensor.
- The air pressure sensor is a control sensor that achieve induction control based on air pressure that is a conducted object. Inside the air pressure sensor, there is an intake pipe introducing air to enter the sensor. Once energized, it is able to transfer air into the interior of the pressure sensor. When the air enters, it will generate a pressure to extrusion the sensor. By capturing the value of current inside the circuit, it is possible to transmit electrical signals indirectly by the pressure value. In this way, the working signal of the device controlled by the air pressure sensor can be sent to make a certain action, and finally complete a set of work.
- In the structure of the air pressure sensor, the vacuum tube is connected to the intake manifold. The engine senses vacuum changes in the intake manifold with different speed loads. Then converts the change in the internal resistance of the sensor into a voltage signal. This signal provides a reference for the ECM computer to correct the fuel injection volume and ignition timing. In other words, the ECM computer outputs 5V voltage to the intake pressure sensor. Then signal terminal will detect the voltage value. When the engine is in an idle state, its voltage signal is about 1-1.5V. When the throttle is fully open, there is about 4.5V voltage signal.
- When an internal combustion engine or the like is started, air is required to enter so that fuel such as gasoline can be ignited. So how much air do it need to inject? It requires the use of an air pressure sensor for control. When the air is injected into for a certain amount, the pressure generated will reach a certain level. When the level is met, the air pressure sensor can use the signal to stop the air from entering. In this way, the system can complete the ignition work.
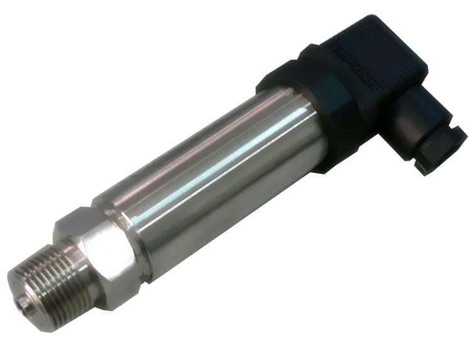
- Precautions for air pressure sensor use
Therefore, the user must pay attention to maintain the pressure sensor during use. Although the pressure sensor has a stainless steel housing, it is still easily damaged. In particular, some improper operations will easily cause damage to the pressure sensor.
1. Using the air pressure sensor over the measuring range
In general, the use of pressure sensors in overrange is the principal cause for sensor damage. Do not apply pressure to the pressure sensor that exceeds the rated withstand pressure. If a pressure higher than the withstand pressure is applied, it is highly likely to cause breakage.
2. Use environment of the air pressure sensor
Second is the use environment of the air pressure sensor. Avoid using pressure sensors in environments with flammable and explosive gases. If pressure measurements are required in high temperature, humidity, and harsh environments, must use special types of pressure sensors to adapt to the changes in environmental conditions.
3. Power supply voltage and load short circuit
The problem of power supply voltage and load short circuit must also be noted. Do not exceed the rated voltage range when using the air pressure sensor. If a voltage exceeding the rated voltage range is applied, the sensor may be broken or burnt. In addition, avoid shorting the load, otherwise it will also cause the pressure sensor to rupture or burn. There is a point that easily be overlooked is incorrect wiring. Avoid incorrect wiring for the polarity of the power supply.