What is a Pressure Sensor
A pressure sensor is also called pressure transducer, which is a device or equipment that senses a pressure signal and converts the pressure signal into a usable output electrical signal according to a certain law.
The pressure sensor are usually composed of pressure sensitive components and signal processing units. According to different measured pressure types, the pressure sensor is generally divided into gauge pressure sensors, differential pressure sensors and absolute pressure sensors. According to different working principles, it can be divided into many types of sensors, the most common type are diffused silicon pressure sensors and monocrystalline silicon pressure sensors.
Pressure sensor are widely used in industrial control system, automotive, medical equipment, Food production, aerospace, military industry and other fields. Want to
buy affordable pressure sensor? please go to
ATO.com online store.
The calibration for the differential pressure transducer mainly includes range adjustment and zero migration. To ensure the normal operation of the differential pressure transducer and the accuracy of differential pressure and flow measurement, users need to periodically check and calibrate it. The differential pressure transducer has a positive pressure terminal and a negative pressure terminal. In general, the pressure at the positive pressure terminal should be greater than the pressure at the negative pressure terminal so that the measurement can be performed normally. In the actual calibration process, users often mistake that the range of the differential pressure transducer can be changed by the HART communicator, and the zero point and the range adjustment can be performed without inputting the pressure source. In fact, this method only sets the range and does not meet the calibration purpose. The correct calibration should be to use the standard instrument for zero and range calibration in the case of external force, and carry out the necessary range migration according to the actual working conditions on site.
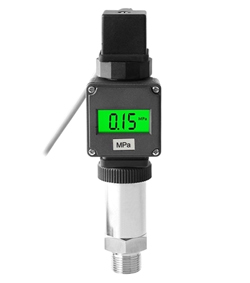
The digital pressure transducer has a LCD screen with backlight, which can display pressure values in real time. It uses DC 24V / 12V as the power source, converts the pressure signal into current signal (4-20mA / 0-20mA), voltage signal (0-5V / 1-5V / 0-10V) or RS485 signal to output. The pressure transducer is small in size, light in weight, and has high anti-vibration and anti-shock performance. It can measure the pressure for air, steam, hydraulic and high temperature liquids. Measuring range -0.1~100MPa / -1~1000bar / -14~14503psi, medium temperature -40~ +60℃ (-40~ + 140℉).
In the linear range of the pressure transducer, the higher the sensitivity, the better the measurement result. For pressure transducer with high sensitivity, the output signal corresponding to the pressure change is more pronounced, which is advantageous for signal transmission. However, if the pressure transducer sensitivity is too high, external noise unrelated to the measurement will be mixed in.
The connection method of the pressure sensor generally include two-wire system, three-wire system, four-wire system, and some sensors have a five-wire system.
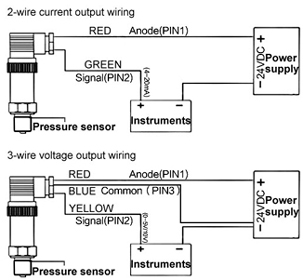
The two-wire pressure sensor is relatively simple, and customers generally know how to wire. Connect a line is to the positive pole of the power supply, and the other line that is the signal line connected to the negative pole of the power supply through the instrument. This is the simplest. The three-wire pressure sensor add a wire to the two-wire system. This wire directly connect the negative pole of the power supply, which is more troublesome than the two-wire system. The four-wire pressure sensor has two power inputs and the other two are signal outputs. Most of the four-wire system is voltage output instead of 4-20mA output. The 4-20mA machine called pressure transmitter, and most of them are two-wire system. Some of the signal output of the pressure sensor without amplification. The full-range output is only a few tens of millivolts, and some pressure sensors have an internal amplification circuit, whose full-range output is 0-2V. As for how to connect to the display meter, it depends on how large the meter's range is.
A pressure sensor is a device or equipment that senses a pressure signal and converts the pressure signal into a usable output electrical signal according to a certain law. The pressure sensor are usually composed of pressure sensitive components and signal processing units. According to different measured pressure types, the pressure sensor are generally divided into absolute pressure sensors, differential pressure sensors and gauge pressure sensors.
A differential pressure sensor is also called differential pressure transducer. It is a
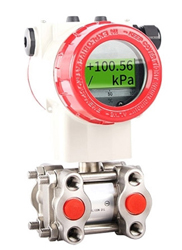
sensor used to measure the difference between two pressures. It is usually used to measure the differential pressure between the front and rear ends of a device or component as well as the differential pressure between different medium in the same process. Its outer casing is made of stainless steel or aluminum alloy. The connecting thread on the pressure tap is NPT1/2. The thread of the output cable connection hole is M20*1.5. Differential pressure sensors are widely used in the production process control such as electric power, coal, spinning cotton boxes, dust removal equipment and other industries.
The pressure of the measuring medium directly acts on the diaphragm of the sensor to cause the diaphragm to generate a micro-displacement proportional to the medium pressure, so that the resistance value of the sensor changes. Then the change detected by the electronic circuit, at the same time, it converts and outputs a standard measurement signal corresponding to this pressure.
For the application of differential pressure sensors, zero migration processing is generally not required if the measurement conditions are enough. However, the differential pressure sensor often takes into consideration for the maintenance and installation during the actual use. In order to facilitate the operation, there is often a horizontal difference between the pressure tapping point and the measuring instrument, or when there are some limiting factors in the measured medium, such as strong corrosiveness, excessive viscosity, etc., this will cause certain obstacles to the whole pressure measurement process, and even affect the measurement accuracy of the meter. Therefore, in order to achieve accurate measurement for the differential pressure sensor as much as possible, the differential pressure sensor zero-point migration technique is usually processed. This paper will conduct a detailed analysis and research on the zero-point migration for differential pressure sensors.
In industrial applications, 2 wire pressure transducers are definitely the first choice. In industrial production, the measuring points are generally on site, and the display device or control device is generally in the control room or control cabinet. The distance between the two will be tens of meters or even hundreds of meters. Eliminating two wires means that the cost can be reduced a lot.
The hydraulic pressure sensor are common applications in most modern water distribution systems. In current industrial applications, pressure sensors and digital pressure gauges are the two most widely used in water distribution systems. A pressure gauge is a meter that measures and indicates fluid pressure with a resilient element as a sensitive component. Pressure gauges have existed for centuries and have proven to be accurate and reliable. Compared to the characteristics of the pressure gauge not outputting the signal, the pressure sensor converts the measured pressure into a standard current signal output.
Differential pressure sensor is a kind of instrument widely used in industrial production. It can measure many physical parameters. The pressure of gas and liquid can obtained by differential pressure sensor, which is of great significance for industrial production.
The 2-wire, 3-wire, and 4-wire of the pressure transducer refer to the wiring of the transducer. This title appeared only after the birth of the two-wire pressure transducer. It is the result of the widespread use of electronic amplifiers in the measurement of pressure sensors. The essence of amplification is an energy conversion process, which is inseparable from the power supply. Therefore, the first to appear is the four-wire pressure transducer. In this system, two wires are responsible for the supply of power, and the other two wires are responsible for outputting converted and amplified signals (such as voltage, current, etc.). The appearance of the electric unit combination meter made the four-wire pressure transducer has been widely used. The transducer’s power supply is 220VAC, and the output signal is 0-20mA DC.
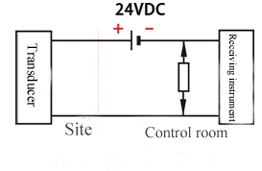
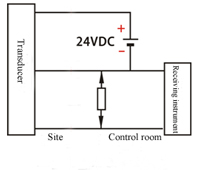
Piezoresistive pressure sensors are pressure sensors made by using the piezoresistive effect of monocrystalline silicon materials and integrated circuit technology. The sensor use monocrystalline silicon wafer as the elastic component. Using an integrated circuit process on monocrystalline silicon wafer, a set of equivalent resistance is diffused in a specific direction of monocrystalline silicon. The resistor are connected into a bridge and the monocrystalline silicon wafer is placed in the sensor cavity. When the pressure changes, the monocrystalline silicon strains, so that the strain resistance directly diffused on it generates a change proportional to the measured pressure, and the bridge circuit obtains the corresponding voltage output signal.
It is very necessary to research the installation before the pressure sensor is officially put into operation. In order to make the pressure sensor reach the measurement accuracy, in addition to the correct selection and calibration, it is also necessary to pay attention to the correct installation of the entire system. The correct system installation includes the opening position of the pressure inlet, the proper laying of the connecting duct, and the mounting position of the meter.
Pressure sensors often occurred in failure during use due to some reasons. The reasons may be the user' s own use method is inappropriate, or the external environmental factors have changed, or the quality of the sensor production is not enough, etc., which may cause the pressure sensor to failure. Here are some of the most common failures and solutions for the pressure sensor, so that everyone can find the problem rapidly.
Calibration is the process for adjusting the electrical signal of the pressure sensor to have a known relationship to the measured pressure. The pressure sensor must connect with the instrument for work after the calibration is completed, otherwise the required accuracy cannot be achieved and the pressure reading cannot be obtained correctly. This article will share the calibration process for pressure sensors. Each step in the process has different calibration items and technical standards.